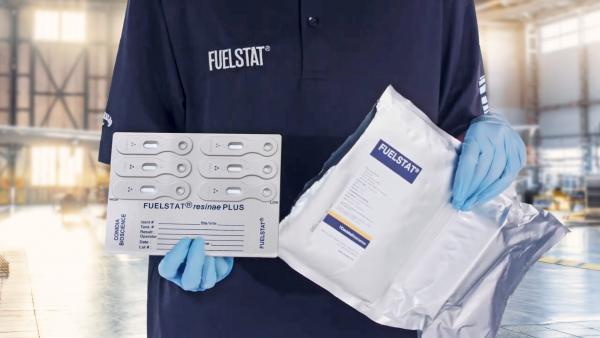
-- It’s imperative to have a secure power supply within a hospital environment and can be a matter of life or death. If there is an outage, even for just a few minutes, it can have adverse affects on patients especially on life support who require their equipment to be fully operational. It is for this reason that almost all hospitals worldwide have some form of emergency backup generator which is more often than not powered by diesel.
Just one single tank of diesel has the capability of maintaining power to the hospital for approximately eight hours however there are some concerns that have been flagged about the reliability of backup generators after it’s been reported diesel generators can be susceptible to fuel blockages. These fuel blockages are caused by a phenomenon known as microbial contamination (diesel bug) which blocks fuel lines with microbes (such as fungi and bacteria) that can grow in tiny microscopic water that is entrapped within diesel fuel. Over time as generators aren’t fired up frequently enough, the microbes are allowed time to grow with potentially devastating effects.
So if there is a real risk of microbial pollution in the supply of biodiesel to emergency generators, what precautions are taken? Unfortunately the risks associated with the ‘diesel bug’ only work their way into service guidance from manufacturers of generator equipment. In industries such as aviation and marine, the risk posed to equipment is well recognised, but awareness is not as high among hospital operators, who rely instead on the expertise of fuel maintenance contractors who charge hospitals for fuel polishing.
Therefore, it is wise for certain contractors to carry out testing and to provide operators with reports as fuel quality verification. In 2016, the British Standards Institute replaced BS5410-3:1976 with an updated release to address concerns over critical standby generators failure. Guidelines in the new standard consider how the life cycle of fuels has declined since the introduction of biofuel and state that: ‘Fuels for emergency generators should be tested for consistency and suitability every six months if they are fitted with a fuel polishing system, if there is no polishing system, the fuel should be tested every three months. Read more from the original Hospital Times article here: https://www.hospitaltimes.co.uk/the-diesel-bug-that-can-give-hospitals-a-generator-emergency/
If samples are being taken offsite for testing, this ideally needs to happen within hours as when samples are preserved in transit, the microbial community may change and therefore the test results may not be representative of the microbial growth in the tank/generator. The Standard Guide for Microbial Contamination in Fuels and Fuel Systems, ASTM D6469 – 14, states in Section 8.5 that: “Samples for Microbiological testing should be kept on ice for transport to the laboratory. Tests should be performed within 4 h and no later than 24 h after sampling. Samples stored at higher temperatures, or for longer times, can show the presence of microbial contamination that does not represent actual fuel system conditions.” Overall, it would make much more sense to carry out testing onsite to avoid these issues altogether. This can be achieved using an immunoassay antibody test kit such as FUELSTAT® from Conidia Bioscience.
Find out more about Conidia and Fuelstat here: https://conidia.com/
Release ID: 88976162